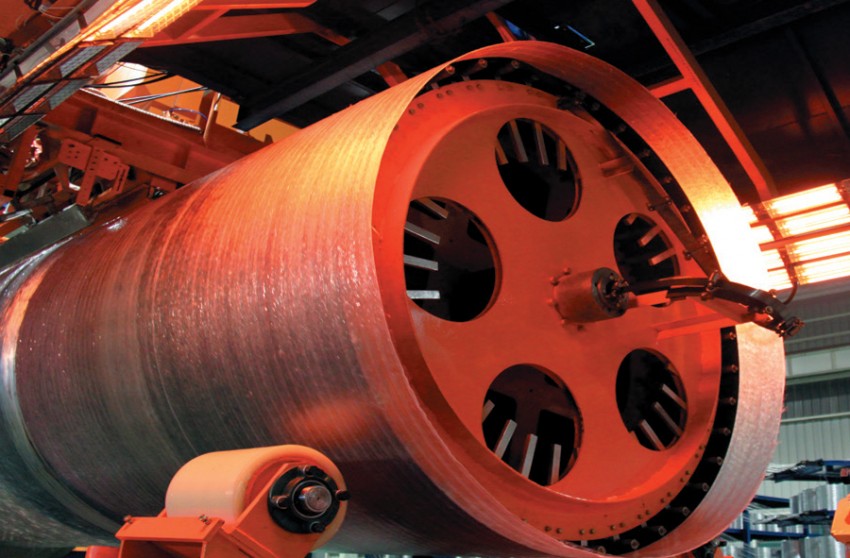
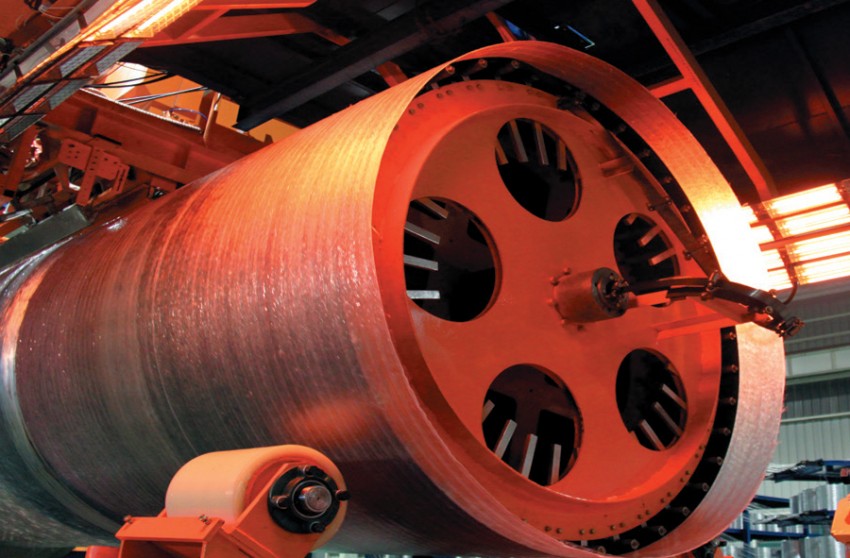
FRP pipe has many applications in industry and infrastructure where easy-to-install, durable, long-lasting pipes and fittings are required, such as petroleum marketing, municipal and industrial services, and on oil and gas fields. In many sectors, FRP pipe is becoming the preferred choice over concrete piping as it is more durable and resilient to corrosion.
The product has been with us for almost seventy years, with manufacturing standards dating back as far as 1959. Traditionally, FRP piping is manufactured by the continuous winding of fixed length glass filaments around a core mould and bonding them together with epoxy resins. The resins undergo irreversible chemical reactions as they cure resulting in pipe with enhanced performance, lighter weight, and greater mechanical capability than non-reinforced thermoplastics.
However, the traditional manufacturing process is labour intensive and slower than the process we have developed, which allows for highly efficient continuous production of pipe at greater speeds with less labour. This process also removes the limitation of having to make FRP pipe to a standard length and has a low loss of raw materials, meaning very little waste when considering environmental concerns.
The finished FRP pipe equals its traditional counterpart for reliability and performance, with a maintenance free service life of up to 70 years. It has all the usual benefits expected of FRP pipe: high axial strength, corrosion resistance, cost-effective to transport and install, and good sealing performance. In addition, we can make FRP pipe to any length, faster and at a lower cost.
More than being an innovative product, this demonstrates how China is leading the way internationally in the production methodology of glass pipe technology. Contact us if you would like more information.